This Month in Food Safety News (September 2020)
Decon7 Team • September 30, 2020
As the global pandemic continues, many businesses are pivoting. Garment manufacturers are making face masks, distilleries are making hand sanitizer, and restaurants are finding new and creative ways to stay afloat with limitations on how they are allowed to operate. With a product that kills viruses at the RNA level, Decon7 was already well positioned to expand operations in order to meet the increased demand for disinfectants and hand sanitizers.
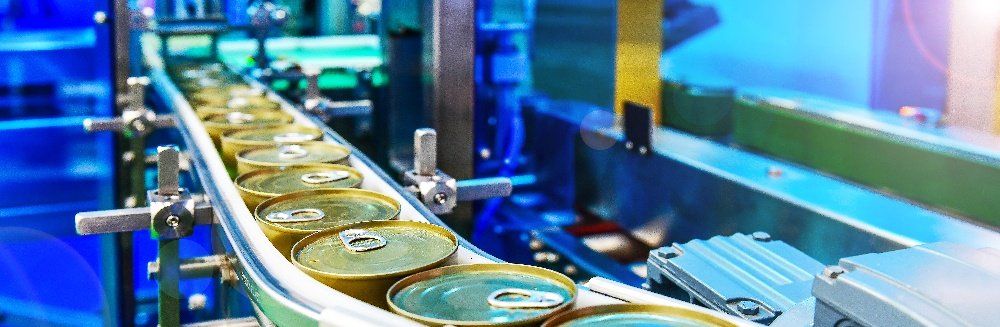
There has been a longtime mystery for the so called “invisible barrier” left behind resisting microbial growth on surfaces treated with Decon7. These surfaces or substrates include but not limited to the following; Carpet, clothing, brick, vinyl (fences, siding, curtains – poultry barns), cement, stucco, all wood for construction, HVAC ducting, evaporator coil pans, sheetrock, filter material, etc. Unlocking the mystery has been quite puzzling and from recent lab testing done some discoveries have taken place to explain this chemical reaction; Firstly the Part I formulation has an extensive ingredient list (proprietary), and there is one ingredient that has decomposition properties. Secondly the Part II is mainly H2O2 – 7.9% Hydrogen Peroxide which has penetration and oxidation properties. When the 2 parts come together they create a completely different action than if they were applied separately. Part I has decomposition capabilities within the main ingredients, this decomposition action begins to take place from the Part II joining. The reactivity and “dwell” time of the 2 formulations mixed eventually breaks each formulation down to the so called “barrier”. During this “dwell” time the 2 parts are capable of penetrating spore walls and destroying the mycotoxins or cytotoxins within the spore. Because of this it becomes extremely effective when used in a fog application. The fog or mist is atomized to a small enough micron to hang in an air space long enough to degrade and destroy any airborne spore or surface mold spore or colony. The so called “barrier” is the resulting chemical reaction of the 2 components degrading each other to the point of making a “hardened” surface, mostly of an Alkali and peroxycarbonate. A portion of the alkali (carbonate) rearranges in such a manner to form a water insoluble compound. This compound “barrier” creates an alkaline surface with a pH high enough - (pH of over 8), to deter and inhibit growth of microorganisms. This resulting barrier would also be able to be classified as a “green” final composition given the decomposition of most initial ingredients. And the so called “residue” left behind would be classified as a mined substance. The benefit of such an “invisible barrier” would be the fact that it would be completely non-toxic, extremely resistant to microorganism growth, mold and algae. The real benefit is while the 2 parts are active (8 to 12 hours) it becomes deadly to any spore, bacteria, virus or microorganism. And having this product also capable of creating a “zone of inhibition” it really becomes a standalone 2 part formulation unlike anything on the market. Treating substrates such as sheetrock paper, plastics, vinyl, or even air filtration material become reality, and now to claim not necessarily killing microorganisms, but creating a barrier that is resistant for any growth and is water insoluble is quite remarkable. Decontamination and cleaning test sites on roofs, decks, siding, (vinyl & stucco) have been ongoing for up to 4 years. Also remodel projects with moisture intrusions creating mold issues have been conducted. There has been no recorded re growth of any mold or algae on any surfaces treated with the Decon7 formulations. Mold remediation in homes and commercial properties using Decon7 is in the hundreds of thousands of square footage treated by the fogging and spraying method. Industrial Hygienists have been engaged for testing spore activity before and after, resulting tests have indicated the non-viable spore counts to be near zero on most sites. The residue is nontoxic, nonflammable and completely environmentally safe. With comparisons being made daily to all other products on the market – there has not been one that can claim these safety standards and perform even close to our Decon7 line of products. 長期以來,人們一直對所謂的“看不見的屏障”感到困惑,因為3D處理的表面上屏障微生物無法抵抗及生長。 這些表面包括但不限於以下; 地毯,衣服,磚,乙烯樹脂(柵欄,壁板,窗簾-家禽舍),水泥,灰泥,所有建築用木材,HVAC管道,蒸發器盤,薄板岩,過濾材料等。 最近的實驗室測試做了一些發現,可以解釋這種化學反應。 首先,Part1具有豐富的成份具有分解獨特性。 其次,Part2主要是H2O2-7.9%的過氧化氫,具有滲透和氧化性能。 當兩個部分放在一起時,它們將產生與單獨應用時完全不同的動作。 Part1在主要成分內具有分解能力,這種分解作用從Part1的加入開始發生。 混合的兩種製劑的反應性和“停留”時間最終使每種製劑分解成所謂的“屏障”。 在此“停留”時間內,這兩個部分能夠穿透孢子壁並破壞孢子內的真菌毒素或細胞毒素。 因此,當用於霧化應用時,它變得極為有效。 霧或霧被霧化到足夠小的微米程度,以在空氣空間中懸掛足夠長的時間,以降解並破壞任何空氣傳播的孢子或表面黴菌孢子或菌落。 所謂的“屏障”是兩種組分相互降解到最終形成“硬化”表面的化學反應,主要是鹼和過氧碳酸鹽。 這種化合物“屏障”可形成鹼性表面,其pH值足夠高(pH值超過8),可以阻止和抑制微生物的生長。 考慮到大多數初始成分的分解,由此產生的屏障也可以歸類為“綠色”最終組成。 留下的所謂“殘渣”將被歸類為礦物質。這種“隱形屏障”的好處是它完全無毒,對微生物的生長,黴菌和藻類具有極強的抵抗力。 真正的好處是,當這兩個部分都處於活動狀態(8到12小時)時,它對任何孢子,細菌,病毒或微生物都具有致命性。 而且,由於該產品還能夠產生“抑制區域”,因此它實際上成為了獨立的兩部分配方,與市場上的任何產品都不一樣。 處理諸如薄岩紙,塑料,乙烯基或什至是空氣過濾材料之類的基質已成為現實,現在聲稱不必殺死微生物,但創造出一種對任何生長都具有抵抗力且不溶於水的屏障,這是非常顯著的。 屋頂,甲板,壁板(乙烯基和灰泥)的去污和清潔測試場地已經進行了長達4年。 還進行了帶有潮氣侵入而導致發霉的重塑項目。 在用3D配方處理過的任何表面上,沒有任何黴菌或藻類再生的記錄。 使用3D對房屋和商業物業中的黴菌進行修復的方法,是通過霧化和噴塗方法處理的數十萬平方英尺。 工業衛生學家之前和之後都參與了孢子活性測試,結果表明大多數地方的無效孢子數都接近於零。 殘留物無毒,不易燃且完全環保。 每天都與市場上的所有其他產品進行比較-尚無一種產品可以聲稱有這些安全標準,甚至可以接近3D這類產品。
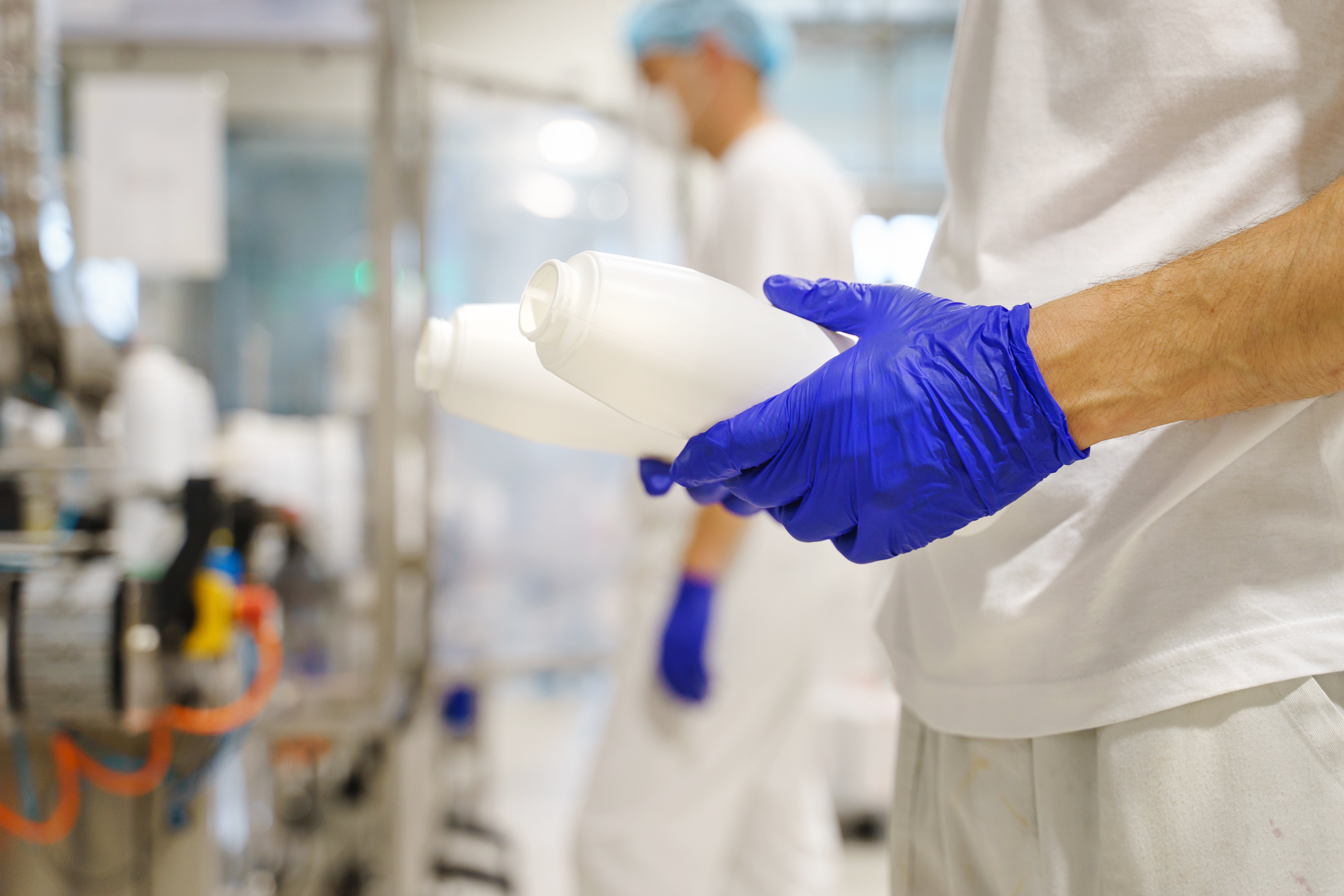
Decon7 has been working hard to expand production in response to increased global demand for disinfectants due to the coronavirus pandemic. In addition to adding six new production facilities, we have also become kosher- and Halal-certified, allowing us to distribute products in even more countries.
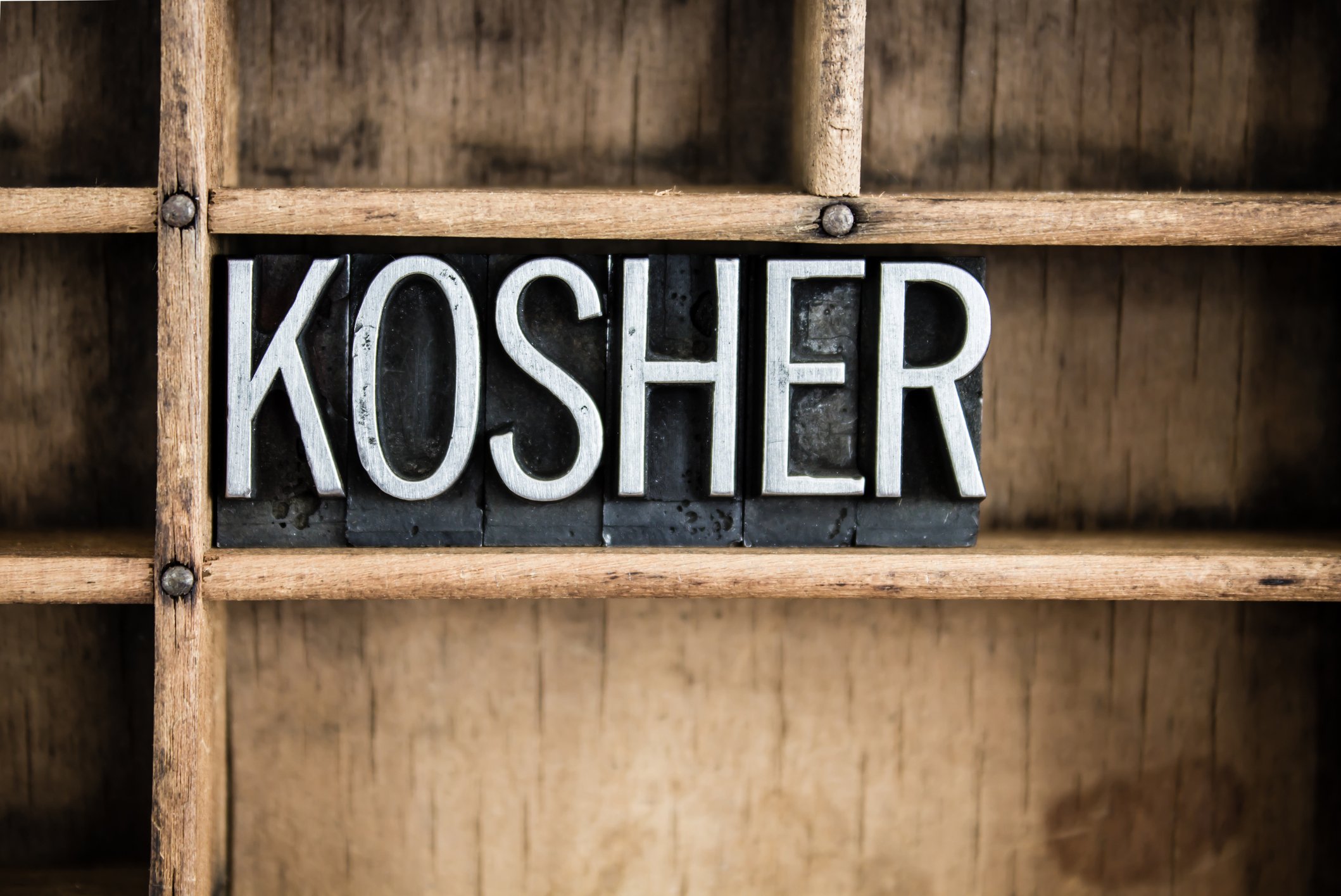
The global pandemic has caused disinfectant manufacturers to scramble to get EPA-approved label claims, and it’s not surprising that many companies have seen a dramatic increase in production. Manufacturing of D7 is no exception. Before the pandemic, D7 was produced in two facilities. Because demand has increased significantly, it is now made in eight different locations.